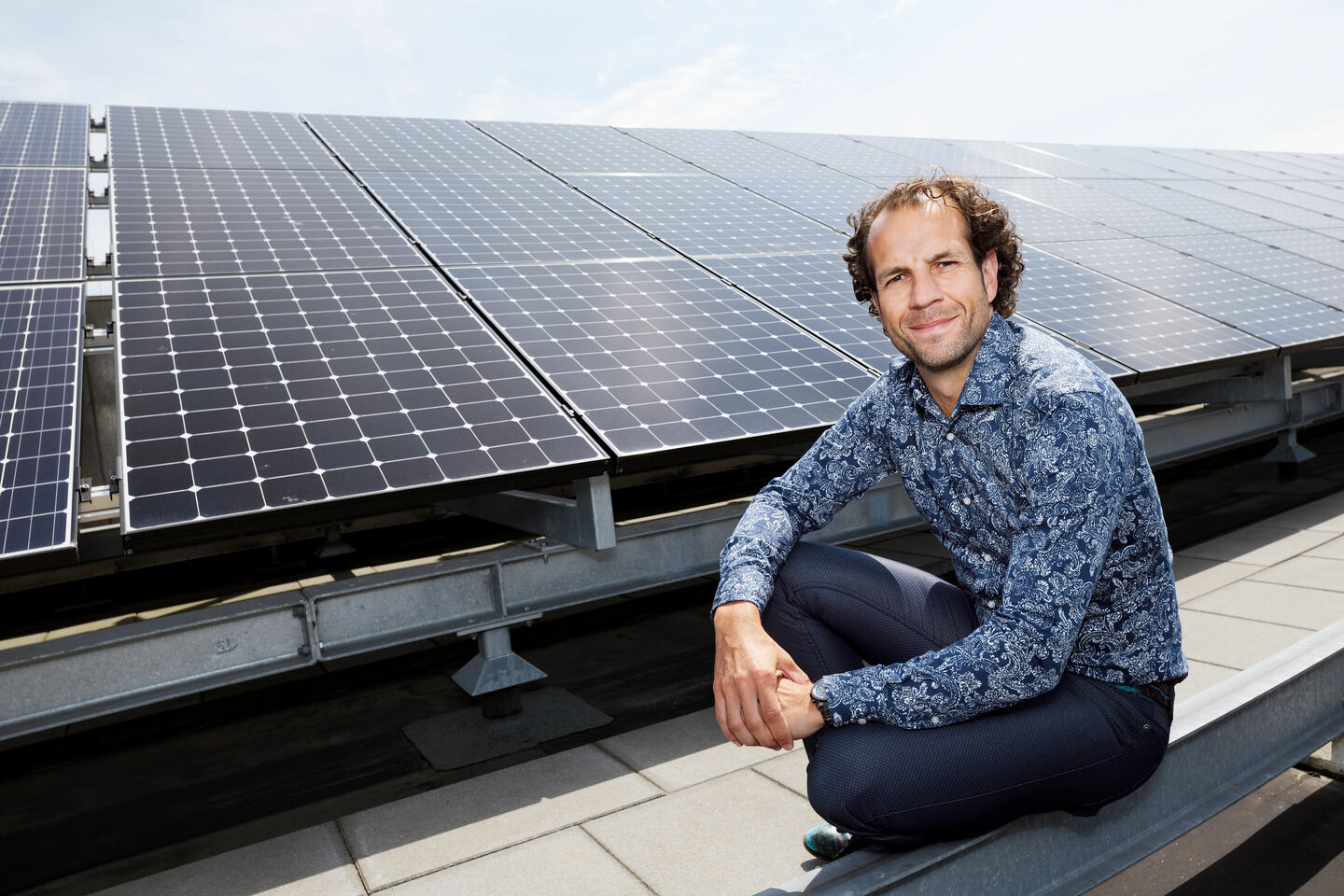
Homegrown solar power
A column displaying four types of solar panel - all four with a touch of TU/e technology - has recently appeared in the hall of Flux. This is the first travelling exhibition in support of 100% Future Friendly, the campaign with which TU/e hopes to make everyone on campus aware of its sustainable initiatives. At the insistence of Professor Erwin Kessels, solar panels of these same four types now cover the roof of Flux. “These panels give us the chance to tell our story.”
“Look over there, at the roof of Spectrum,” says Erwin Kessels, leader of the research group Plasma and Materials Processing, pointing from the third floor of the Flux building. “It's completely covered in solar panels. Wonderful, of course, but those panels aren't linked in any way to the research we are doing here at TU/e. While almost one-third of all new solar panels now contain technology that we have helped develop.”
This is why, when solar panels were subsequently due to be installed on Flux, Kessels went to Real Estate Management (DH) to argue that panels with a TU/e connection should be chosen. “To create a visible sign of what we do as a university; that our research is helping to make the world more sustainable. It would be a shame not to grasp the opportunity.”
In practice solar panels on the roof of a tall building like Flux cannot easily be seen, so the professor also proposed that the university buy one extra of every type of panel used. These now form part of the Road Show for the 100% Future Friendly campaign, a travelling exhibition with a short accompanying film, which is screened alongside the installation, and can also be watched on the internet.
Plasma and Materials Processing is not the only research group at TU/e working on solar cells – another group where solar power is also an important research line is Molecular Materials and Nanosystems, headed up by René Janssen. “But we are closer to the application end,” Kessels points out. Much of his research focuses on improvements to existing silicon technology. Aspects such as special nanolayers that generate a fractional increase on the efficiency. “An additional 1 percent may seem minimal but expressed in monetary terms in such a large industry it's a gigantic difference.”
Below, we give an overview of the four types of solar panels and the underlying techology.
IBC: contacts on the rear
The first panel to be exhibited has previously been put to use for Stella, the solar car created by Solar Team Eindhoven, explains Kessels. “You can see that the cells are completely black: all the electric contacts are on the rear side. These are Interdigitated Back Contact (IBC) cells in the jargon. They capture that little bit more sunlight. In addition, they are almost black, which shows that they reflect little light, which is also advantageous, of course.” For comparison he picks up a wafer of pure silicon. “Look, it's a mirror of sorts. To prevent sunlight reflecting off them, all solar cells have an anti-reflection layer.”
The method used by the manufacturer of these IBC panels, Sunpower, to apply the anti-reflection layer is based on a technique that Kessels himself developed while a PhD candidate at TU/e - a deposition method using what is known as expanding thermal plasma. “These are the most efficient solar cells you can buy, with a return of more than 24 percent.”
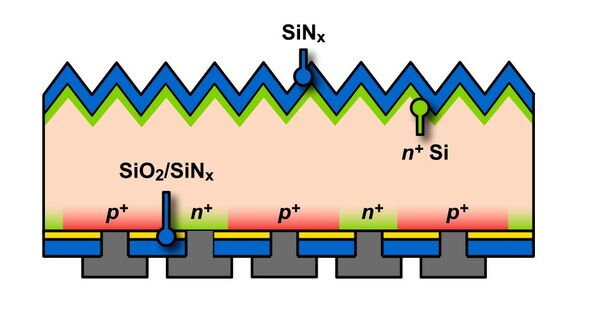
PERC: efficient due to passivation
The second panel makes use of a revolutionary technique called PERC, Passivated Emitter Rear Contact. Basically, a wafer-thin layer of material is applied to the base of the cell, between the metal that serves as an electrode and the silicon in which electrons are released when exposed to sunlight. This layer prevents the free electrons being lost in the transition between silicon and electrode.
“Passivation is the name of this process,” says Kessels. “We demonstrated in 2005 that a nanolayer of aluminum oxide does the job well. This was picked up by Q Cells, one of the market leaders in solar panels. One-third of new solar panels now contain aluminum oxide. Without our contribution that would likely not have happened, although of course you never know how things would have gone.”
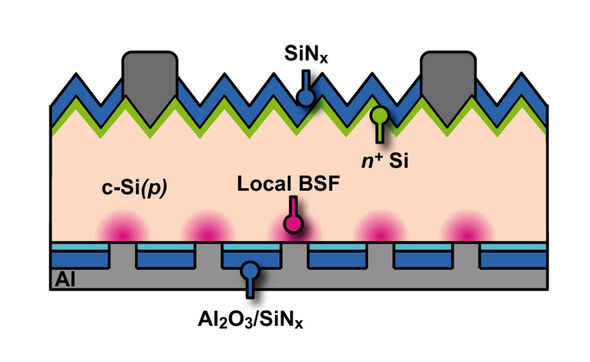
SHJ: no direct contact
The third solar cell contains even more sophisticated technology, thanks to which the passivation is achieved by a series of thin layers of a substance called amorphous silicon that lie between the crystalline silicon and the electrode. “With PERC you still have to produce a grid of contact points, but with this Silicon Heterojunction (SHJ) there isn't any direct contact at all between the crystalline silicon and metal electrodes.”
The SHJ cells on the roof of Flux give a return of 19 percent, but the laboratory record for this technology far exceeds 26 percent, Kessels explains. “Think of these panels as a first version. We've recently had a few projects of our own involving SHJ cells, and it's an area we'll continue to work on in the coming period. It is a technology for the future.”
The aim moving forward, he believes, is not only to design more efficient cells, but also to ensure that making them becomes easier – and cheaper. “However fabulous your new solar cell is, if producing it involves too much work, it is a technology that can't compete.”
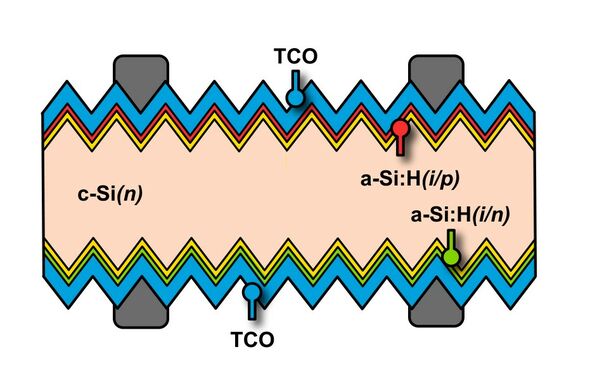
CIS: thin film
Finally, there is what is known as the thin-film cell, unlike the other panels not made from silicon, but from copper indium selenide (CIS). “A cell a few micrometers thick can absorb just as much light as a 200-micrometer thick wafer of silicon. This means the material can be applied to flexible foils, and that in itself offers a host of application possibilities in the built environment.” Moreover, in principle thin-film cells are cheaper to produce than silicon. For the time being, however, with a return of about 15 percent they are being outstripped by silicon cells, the price of which has fallen considerably in recent years.
Kessels' own research group is working on thin layers to order to make a cell using CIS as its basic material, he explains. “We apply nanolayers of, say, zinc oxide or aluminum oxide to collect charge carriers from within the cell. We are doing this as part of Solliance, a cooperative alliance with partners including TNO and IMEC that has laboratories on the High Tech Campus.”
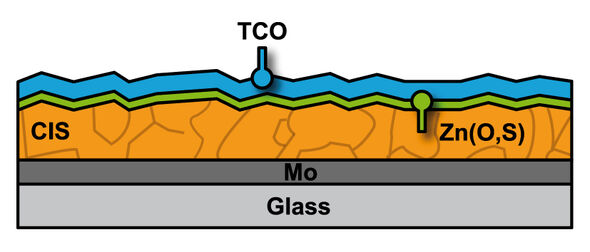
Discussion